Introduction
Animal feed plays a crucial role in the health and well-being of farm animals, as well as the quality and safety of the products that we consume from them. However, the production of animal feed can be a complex and costly process, with many variables to consider. One way to improve the consistency and efficiency of animal feed production is through frequent analysis of feed ingredients. This involves regularly testing and evaluating the nutrient content and quality of the raw materials and additives used in feed production, to ensure that they meet the desired standards and requirements.
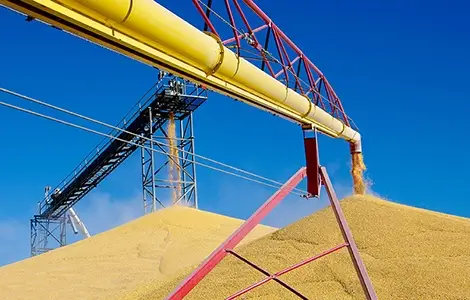
The Benefits of Feed Ingredient Analysis:
- Quality control: By analyzing feed ingredients regularly, feed manufacturers can identify any deviations from the desired nutrient profile and take corrective action if necessary. This helps to ensure that the final feed product is consistently high in quality and meets the nutritional requirements of the animals.
- Cost optimization: Ingredient analysis can also help feed manufacturers optimize their production costs by identifying the most cost-effective sources of raw materials and additives. For example, if a particular feed ingredient is found to be of lower quality than expected, the manufacturer may choose to switch to a different supplier or substitute the ingredient with a more cost-effective alternative.
- Food safety: Regular feed ingredient analysis can also help to reduce the risk of contamination or other safety issues in animal feed. For instance, if an ingredient contains harmful contaminants or adulterants, the manufacturer can take steps to prevent it from entering the feed supply chain.
Designing an feed Ingredient Analysis System
Animal and pet food manufacturers use various feed ingredients to produce feeds with a consistent nutrition profile. For complete oversight of the feed formulation process, the ingredient analysis system should have the following features:
- Be able to analyze feed ingredients and finished feed for major constituents such as protein, fat, fiber, and moisture.
- Be accurate and precise
- Require minimal sample preparation
- Be easy to perform and require little training
- Return rapid results for responsive quality control
Bench NIR analyzers have been used for more than 25 years as a reliable tool for feed manufacturers to monitor the quality of incoming raw materials and formulate consistent compound feed. However, bench NIR instruments have several limitations, including:
- They are expensive($40k+)
- Most require a stable platform in a laboratory-type environment
- Lab instruments require training for the operators
- Most companies have only one bench NIR, so there is time and effort to bring the samples to the instrument and to return the data to the production line.
In addition to the limitations above, there is a resource cost and time delay when testing samples with a bench NIR instrument. The analyst needs to:
- collect and label the sample
- bring the sample to the NIR instrument and place it in the sample queue
- analyze the sample
- report the results
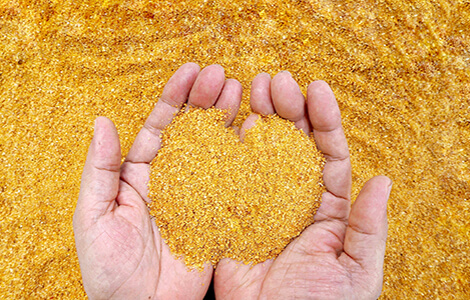
Representative Sampling
The more difficult it is to select a sample, analyze, and obtain results, the less likely this will happen in a busy feed mill when employees are tasked with multiple responsibilities. This negative incentive is contrary to the needs of the production and quality managers, who require the best and most granular insight possible to capture and react to variations in feed ingredient quality.
To maximize the utility of the data collected, the samples analyzed must be representative of the variations found in the process as a whole. Kim H. Esbensen et al. have published a compilation of articles discussing the Theory of Sampling that can be found as an open-access article Representative Sampling for Food and Feed Materials: A Critical Need for Food/Feed Safety1. This topic is very complex and cannot be addressed here. Still, this series of articles provides many good examples and designs to help quality managers design sampling protocols that reveal variation representative of the entire production process. What is needed is a fast, simple, and accurate means to obtain quality data that will facilitate frequent testing and not create negative incentives.
Lowering the Analytical Testing Requirements to Increase Sampling
A proven method to improve testing in a production facility is to reduce the resources required to complete the test. With a simplified testing procedure, plant managers no longer need to compromise on testing frequency.
Easy-to-use portable analyzers are ideal for this situation, as it allows the quality manager to:
- Provide multiple analyzers that can go to where the samples of feed ingredients are
- Use every member of the plant operations team as a quality analyst
- Easily scan many samples of feed ingredients for a complete picture of production conditions
- Obtain instant results for the most critical parameters
- Share data in real-time via a cloud portal
Conclusion
Frequent analysis of feed ingredients is an essential aspect of animal feed production, as it helps ensure the final product's consistent quality and affordability. By regularly testing and evaluating the raw material and additives used in feed production, manufacturers can identify any deviations from the desired nutrient profile and take corrective action if necessary, optimizing costs and reducing the risk of contamination or other safety issues.
Portable, on-site analyzers can provide accurate and reliable data for plant and quality managers to evaluate feed ingredient quality and produce consistent feed more efficiently.
1 Kim H Esbensen, Claudia Paoletti, Nancy Thiex, Representative Sampling for Food and Feed Materials: A Critical Need for Food/Feed Safety, Journal of AOACINTERNATIONAL, Volume 98, Issue 2, 1 March 2015, Pages 249–251, https://doi.org/10.5740/jaoacint.SGE_Esbensen_intro